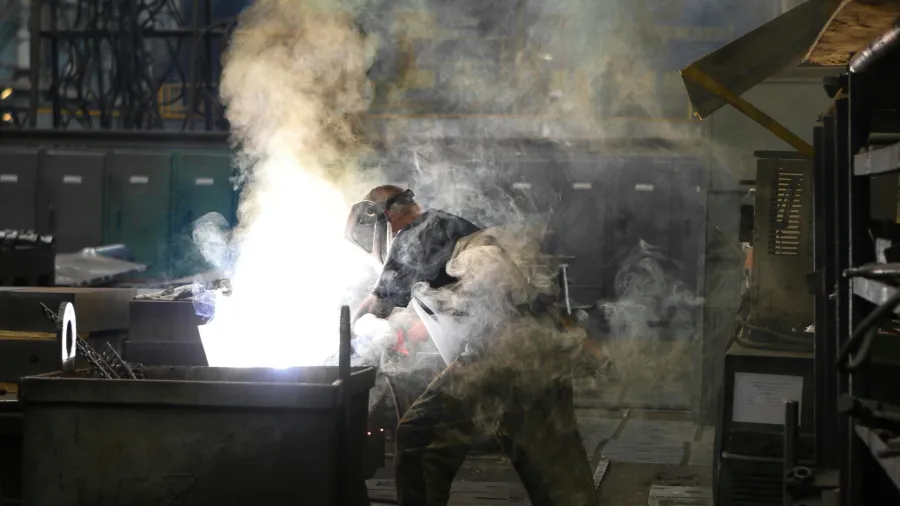
How employee involvement spurs technology integration in manufacturing
A World Economic Forum study unlocks a wealth of ways to improve the technology introduction process and avoid losing employees.
In January, the World Economic Forum (WEF) interviewed 85 frontline workers at eight of the biggest factories in the United States, Europe, and Asia in a bid to unlock a wealth of ways on how to improve the technology introduction process on the shop floor.
The insights gleaned from these interviews sparked understanding that there is a right way of integrating technology in the industrial sector to the utmost benefit of the company and its people.
As was asserted in the WEF’s “Views from the Manufacturing Front Line: Workers’ Insights on How to Introduce New Technology” study, a failed introduction of technology may not only result in increased business costs for the firm, but also lead to it losing its employees.
Whilst it is important for manufacturers to make sure they adopt the latest technologies available, they still need to make sure employees affected are involved in this kind of decision, the WEF report showed.
“You should always listen to [every] person and not listen to [just] the ones you feel comfortable with,” one of the interviewees cited in the report said.
Communication and consultation
The WEF report highlighted how managers are responsible for laying the groundwork for the technology adoption process. Here, they are expected to take time to explain how the decision was made to integrate new technology, why the shift matters, and what expectations are to be hoped from employees.
“There is a need here to ensure that workers (who are often not represented during managerial discussions to review performance) understand both which KPIs (key performance indicators) have been selected and, crucially, why,” the study stated.
“This can help to counter the risks of low motivation and a sense of detachment on the part of workers,” it added.
The company should also help workers explore and become confident working with technology, which can be achieved by conducting regular demonstrations by external providers, and using physical interaction, hands-on exploration, and support videos.
Employee buy-in
Making sure employees are involved is also vital. May it be providing workshops, or assessing risk, making workers feel they belong in the transition gives positive impact.
When it comes to choosing the pilot group, it is important to make sure it will be diverse. This “suggests that an opportunity exists for employers to improve the adoption process simply by increasing the numbers and diversity of workers involved in testing and training,” the report read.
During the process of introducing the technology itself, employers should ensure workers are fully supported whilst adopting technology.
Managers were also urged to set clear timelines as workers welcome assurance that they have sufficient time to familiarise themselves with the new technology.
When it comes to training, the report warned that there is a risk of failure if companies only use one or two training methods. There is a need for a diversified learning programme to cater to different workers who have different learning needs, it noted.
To better curate the programme, the study said companies can use the “live my life” approach. This will involve a white-collar office worker spending a day on the shop floor, performing work tasks, and mixing and talking with workers.
Companies can develop the role of a “super user” or technology champion.” These involve participating in testing and training sessions, developing expertise, being available to answer questions and encouraging peers.
Monitoring and follow-up
Following the introduction itself, the next step for companies is to reach out to their people and follow up. Feedback from employees after a few months of using the technology can help employers know if the programme is effective or is just wasting their time, the report explained.
Companies were also reminded that training is a continuous process. Employers were urged to encourage employees to learn more about the technology. In return, they should listen to workers who have ideas on improving implementation.
“Understanding the perspectives of end users is important. However, to achieve successful technology implementation and adoption – and thrive in the rapidly evolving manufacturing industry – organisations will have to consider employees’ needs beyond augmentation technology and use these insights to develop sound workers’ transformation frameworks,” the study said.
“Only such an integrated perspective will lead to new best practices for human-centric, sustainable and effective technology introductions,” it added.