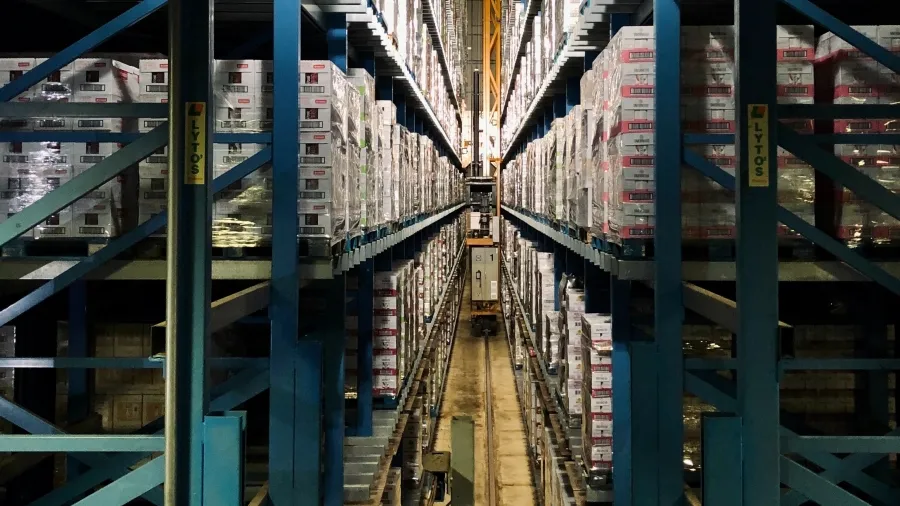
Asia’s supply chains underutilisation hits 2020 low: GEP
Activity in Japan and China are slowing while India performs strongly
Rising production capacity and sluggish demand pushed idle capacity of Asian suppliers to rise at a speed not seen in the past three years, according to a recent industry tracker by GEP and S&P Global.
The GEP Global Supply Chain Volatility Index for Asia slid further to -0.38 in October from -0.20 the month prior, signalling higher idle supplier capacity across the region’s supply chains.
Last month marked the biggest jump in spare supplier capacity for the region since June 2020, as measured by the index, which tracks demand conditions, shortages, transportation costs, inventories and backlogs of factories worldwide on a monthly basis.
A value above 0 indicates higher utilisation and volatility in the supply chains, while a reading below shows underutilisation of production capacity and lower volatility.
The report traced the sharp increase in idle capacity to Asia’s waning economic resilience on the back of weak demand and “falling pressures on factories.” It said Japan and China’s supply chains are losing momentum while India bucks the trend as it continues to outperform.
“The notable increase in supplier capacity in Asia, which was driven by China, provides global manufacturers with greater leverage to drive down prices and inventories in 2024,” said Jamie Ogilvie-Smals, vice president for consulting at GEP.
Globally, the GEP Global Supply Chain Volatility Index fell for the seventh straight month to -0.41 in October from -0.35 in September as spare capacity continues to rise across supply chains, while demand for raw materials, components and commodities remained weak.
Asia recorded the sharpest jump in excess capacity last month, followed by North America’s supply chains whose reading went down to -0.34 in October from -0.30 previously. Both Europe (-0.90) and the UK (-0.93) saw improvements last month but their readings suggest there is still substantial idle capacity in their respective supply chains.