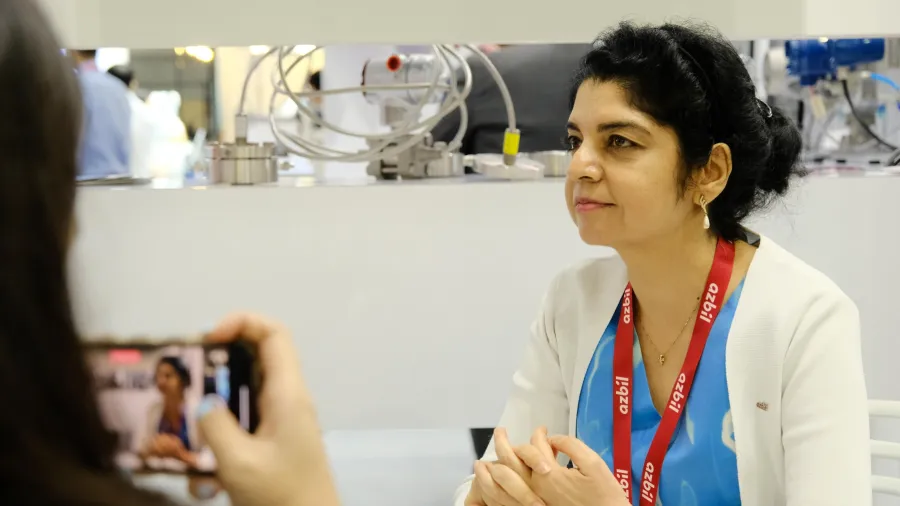
Why digital twin adoption is key in a plant's digital transformation journey
Officials from Azbil said the application targets operations and environmental goals.
Controlling temperature is crucial for manufacturing plants to operate properly, which is why they put importance on monitoring and maintaining their chillers. The job of managing chillers is what Azbil made easier with their chiller plant digital twin application.
In layman’s terms, a digital twin is defined as “a virtual replica of a physical asset”.
In an interview with Manufacturing Asia, Azbil Corporation’s Global Executive Member, Anju Jaswal, explained that their digital twin empowers the user with AI analytics to simulate their chiller plant operations to achieve optimal results.
The user can run simulations using an updated digital twin and test various ranges of parameters and evaluate potential improvement of system efficiency. Operators can apply new parameters with confidence to the real system and gain maximum results.
Azbil Singapore's Business Development Manager, Boyce Fong, added: "Our chiller plant digital twin incorporates built-in AI to empower smart facilities management operations...It also includes a digital sandbox for the user to simulate control strategies and calculate potential savings if the firm wants to improve its building energy performance while also considering occupant comfort."
"There's a machine learning analytics module that enables predictive maintenance by generating an initial model of the chiller plant and using live data to compare against it," Fong added.
The AI continuously updates the digital twin model and assesses for changes in the characteristics of the chiller plants, like declining efficiency.
If such behaviours cross a tolerance threshold, the application will provide the firm’s operations with "actionable insights," like making part replacement or servicing recommendations.
Fong said the data analytics provided by the digital twin to calculate chiller inefficiencies can also help "building owners who have difficulty justifying installing new equipment as an investment worth considering."
The digital twin application is also able to integrate a building information model (BIM) to reduce the labour intensiveness of plant operations.
"As a user, you can have a bird's eye view of the entire facility and its infrastructure layout without having to be physically present, or even printing 2D drawings. You can also navigate the building specifications in first-person view, which offers virtual wayfinding and greatly diminishes the need for time-consuming in-person physical site tours, or even training," Fong said.
Operational goals, however, are not the only targets Azbil's digital twin can achieve.
According to Fong, their digital twin incorporates a green AI engine which allows users to "adaptively control and optimise building energy efficiencies."
"Air-conditioning and ventilation operations are significant contributors to energy consumption in a building. The digital twin allows users to automatically optimise and monitor energy utilisation in real-time," he said.
Using the digital twin, users can also virtually implement control strategies to realise optimal energy efficiency and still satisfy user comfort levels.
"The energy-saving effects can be simulated through energy-saving applications with the digital twin model in cyberspace," Azbil stated on its website.
To add, Azbil's digital twin also contributes to Sustainable Development Goals (SDGs) 9 (industry innovation and infrastructure), 11 (sustainable cities and communities), and 13 (climate action) was adopted by the UN Sustainable Development Summit.
Looking ahead, Fong said Azbil plans to make their digital twin platform available in at least 80% of all applicable buildings in Singapore to contribute to the nation's green plan targets of sustainable development and net zero emissions from future generations.