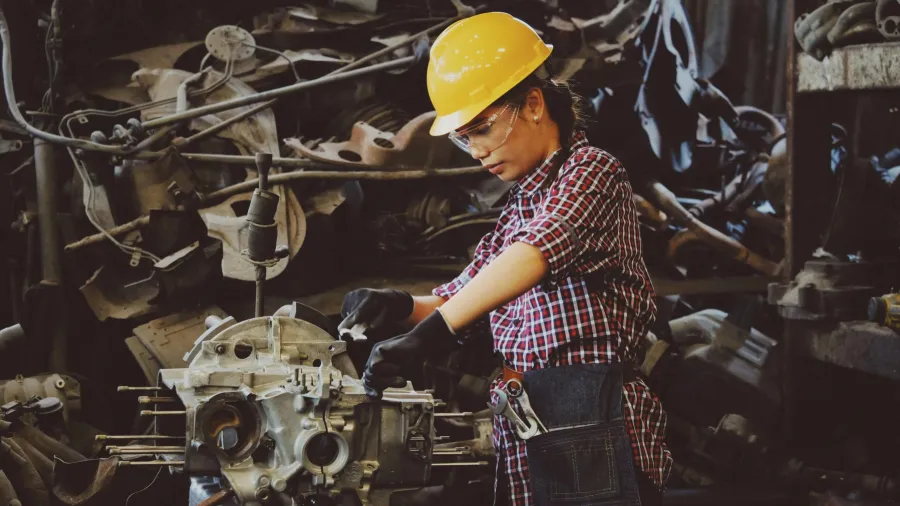
Manufacturers must invest in workforce to boost productivity: report
One hour of unproductive labour per week could cost companies $5,900 annually.
Manufacturing firms must invest in their workforce to boost productivity as they risk considerable value if workforce gaps go unaddressed, according to a McKinsey report.
“In aerospace and defence, a midsize company could avoid more than US$300m in costs and impact to the bottom line by addressing workforce gaps,” McKinsey said.
McKinsey’s research shows that productivity gaps between high and low performers increase by as much as 800% as a task increases in complexity.
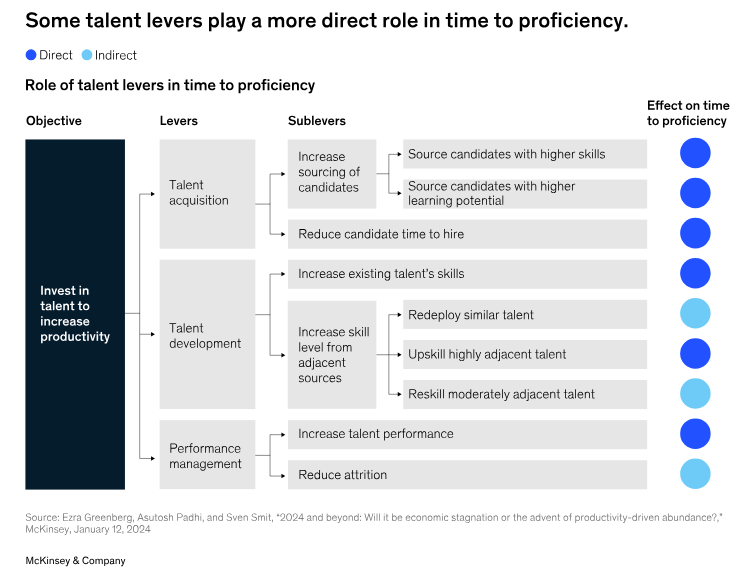
Compared with industry averages, the advanced industrial manufacturers with the highest levels of labour productivity also have the highest levels of total shareholder return, with a difference of 8 percentage points.
McKinsey said one way to address productivity gaps is to start with talent acquisitions. “Manufacturers can drive a more effective talent acquisition strategy by knowing how to better acquire and reduce candidate time to hire,”.
Organisations on the bleeding edge of talent development are also considering holistic programs through coaching, apprenticeship, feedback, and on-the-job learning to tackle the following problem statements:
Moreover, manufacturers must know how they can expand the pipeline of "ready" talent and modernise development approaches that make learning faster and better.
“New insights into what matters most to employees and managerial techniques can make it easier to deliver increased outcomes via similar levels of effort,” McKinsey added.
Additionally, one hour of unproductive labour per week because of lower-skilled employees could cost companies as much as $5,900 annually.
For employers looking to combat their productivity challenges through proficiency, McKinsey noted four moves, including pinpointing the value, rallying cross-functional teams, starting small and piloting solutions, and driving ROI.
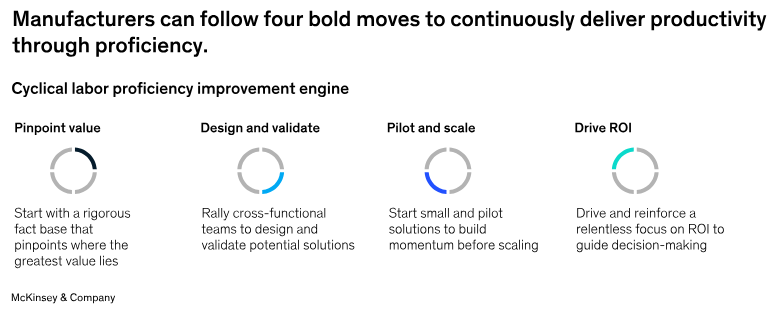