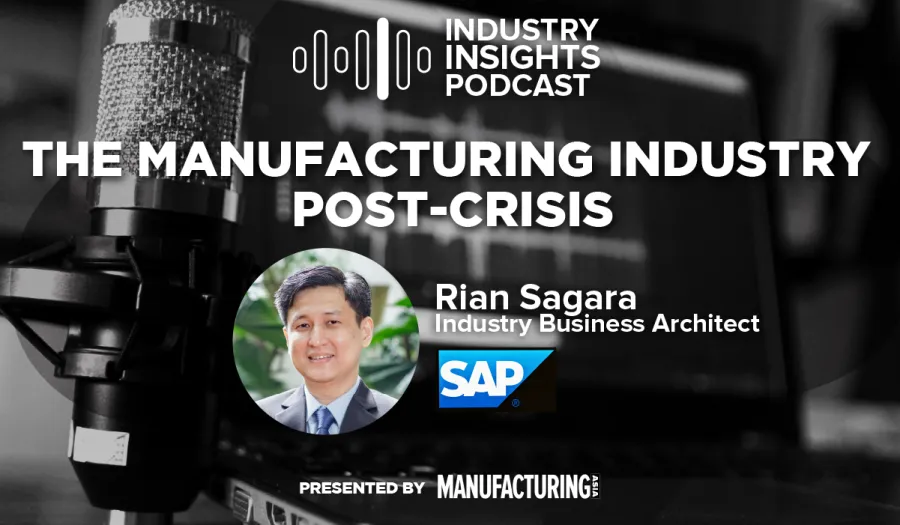
SAP's Rian Sagara shares what manufacturers should prepare for post-disruptions
Rian discussed how Industry 4.0 can help assist businesses in transforming their processes.
Across the world, businesses, particularly the manufacturing industry and supply chains, have been hit heavily by the pandemic. The ability to access, obtain required goods, deliver products to customers, or let alone the ability to adequately manufacture the goods is very different from what the industry players have been used to.
“From having a normal business, the focus now moves to be able to survive, and recover and after the crisis ends, achieve the new business as usual,” Rian Sagara, Industry Business Architect at SAP, said in the second installment of SAP’s pilot series of podcasts - SAP Industry Insights podcast - The Manufacturing Industry Post-disruptions.
“This is led on by the changes of environmental restriction and imposed dynamics such as border restrictions that disrupts supply chain, leading up to the limited resource availability and capacity, thus causing the challenge of resource planning and orchestration,” he added.
Consequently, this might also dictate businesses to juggle across their products and facilities they have or even extending to their partners.
In this session, Rian discussed the trends, shifts, and challenges that have happened in the region’s manufacturing sector since the pandemic, as well as where the manufacturing industry is heading in the post-crisis era.
The manufacturing industry post-crisis
Rian notes that businesses are revisiting their initiatives and priorities as they push their spendings on essentials, whilst putting non essentials on hold.
This is on top of the challenges that manufacturers are facing due to the pandemic such as uncertain supply of critical materials, increased demand, constraint capacity in both manufacturing and logistics, oversteering and intensifying the bullwhip effect, as well as the challenges of manpower like balancing labor shortages and the health and safety of employees.
These are the times where businesses should really identify the shortcomings of their current practice, the areas which should be improved to avoid creating a high cost impact, and identify how they can prevent such loopholes from happening again in the future.
In order to address these, Rian notes, businesses should prepare by imagining a general design to plan and match production capacity paired with real-time simulation capabilities. This will help businesses to decide on how to revamp their operations to match business demands.
Further, having a resilient sourcing and logistic network and the ability to quickly tap into contingent labor and third parties will help ensure production capacity in both manufacturing and logistics. This would ensure the availability of access in the time of constrained capacity and will allow businesses to reconfigure the manufacturing facilities, prioritise the most critical products whilst still ensuring the safety of employees.
Manufacturers are now also looking to move beyond cost and efficiency, and are moving towards quality and customer engagement which would include three key pillars—customer centricity, reinventing production, and end-to-end connectivity.
Rian adds that SAP’s integrated business planning (IBP) can assist manufacturers in running scenario planning, determining the most optimal plan, assessing their capacity requirements, and balancing inventory levels. Their Ariba discovery can also help businesses source availability of supplies as a response to the crisis, thereby speeding up production recovery.
Industry 4.0 heavily supports these objectives by enabling real-time signals through the integrated factory, helping business balance the supply, demand and internal manufacturing process. Businesses will also be able to shuffle the working process, reducing the risk of manpower shortage, as well as the occupational health and safety issues.
Further, it enables businesses to break down traditional silos and provides real-time visibility into inventory, people, and production assets, as well as established digital twins to manage the product life cycle in which businesses can design, manufacture and operate products. Mobile technology, augmented reality, and virtual reality can also be used to train and enable workers to perform tasks more conveniently or even remotely, addressing the issue of lockdown and social distancing.
Benefits of Industry 4.0 in manufacturing
Discover the real benefits of Industry 4.0 for manufacturing in a report from the MPI Group.Download the report.