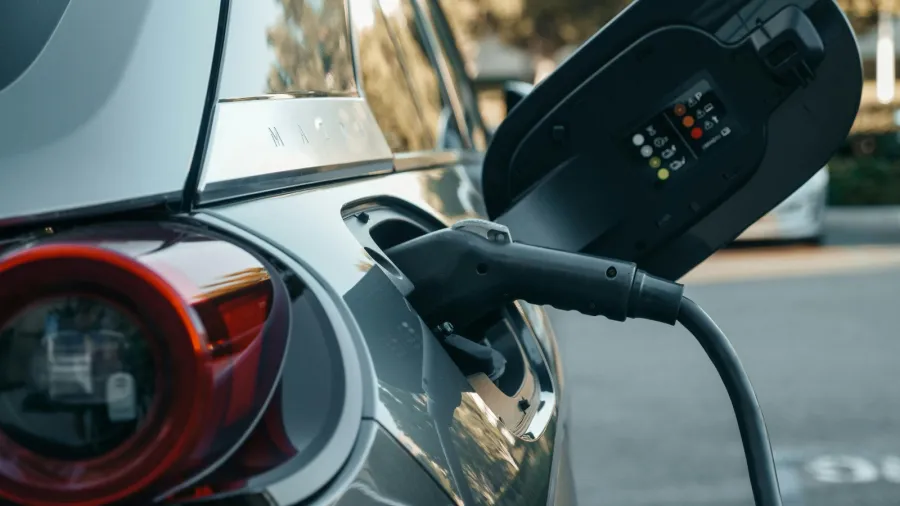
How EV battery manufacturers can overcome cost challenges
Kearney highlighted three ways to reduce production costs.
Amidst challenges in the automotive industry, some EV battery manufacturers have delayed production, cut expansion plans, downsized programs, closed sites, and laid off sections of their workforce, according to consulting firm Kearney.
These could create a new set of problems once the shift to electrification picks up again. Rather than cutting capacities too quickly, Kearney advises battery manufacturers to improve profitability at existing production sites by improving net profit instead of relying on new customers or higher production volume.
Kearney highlighted three methods that offer the greatest opportunities to reduce production costs and improve operational efficiency: streamlining material costs, optimising capex, and implementing innovative processes.
Streamlining material costs
The planning and concept stages offer the most flexibility for major changes. Kearney said it is important to apply technical macro levers such as adjusting general specifications or addressing operating conditions before the battery goes into series development.
Once development begins, this is the time to focus on specific component design modifications, such as producing thinner electrode substrate foils, along with detailed specifications via design-to-X or value analysis and value engineering processes.
Another potential tweak would be increasing the tolerance of non-critical parts, which reduces product costs and creates less waste.
In later stages or after production starts, commercial strategies and AI-driven analytics can revitalise the award process, resulting in up to 10% savings from existing suppliers.
Optimising capex
Kearney’s capex optimisation approach is designed around a comprehensive framework that combines short-term, mid-term, and long-term strategies to sustainably reduce capital expenditure.
Short-term strategies include immediate actions like prioritising projects, leasing machinery instead of buying it and extending the asset lifetime through maintenance, upgrades, or operational adjustments.
Mid-term strategies such as decisions over make-or-buy and tool ownership, along with customer terms and conditions, generally come into play at around the six- to 18-month mark.
Lastly, long-term strategies focus on structural changes such as portfolio role strategies, bundled tool sourcing, and subsidy management to ensure that manufacturers are well-positioned to flex in line with evolving market conditions and advances in technology.
Implementing innovative processes
Two of the most promising in terms of cost reduction are low-solvent coating and dry coating.
Both approaches offer substantial savings by reducing or removing the use of solvents, which shortens drying distances, thus freeing up space in production facilities and reducing their energy consumption.
Other processes that are ripe for improvement are cell formation and cell ageing, which are both capex-intensive due to the resources required to activate, test, and stabilise cells at scale.
By optimising the cell chemistry and applying effective process control, manufacturers could reduce cycle times, along with the equipment and associated capital input needed.