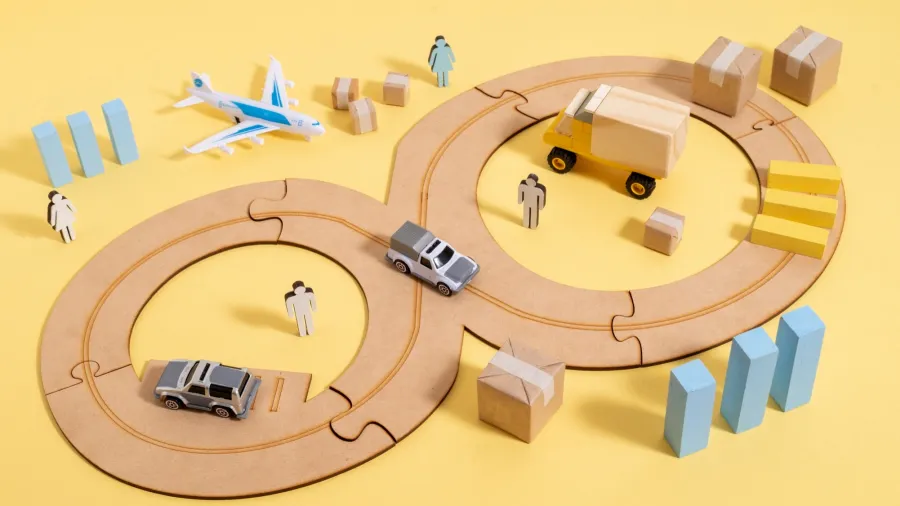
Is forecasting enough to build a resilient supply chain for Asian manufacturers?
By Zhang XinhangA forecast is only as valuable as the supply-chain nerve system that acts on it in real time.
Factory schedules in Asia used to follow predictable demand cycles. That no longer works. Labour, inventory, and transport plans are now routinely upended by sudden order spikes, cancellations, port delays, or trending products.
Forecasting offers limited value when volatility is constant. What matters is whether the supply chain can take the hit and keep moving.
For many manufacturers, forecasting remains the default response. Statistical models are refined, spreadsheets grow more intricate, and historical data sets expand. But recent disruption shows that a brilliant forecast still fails if warehouses, ports, or delivery fleets cannot adjust fast enough. Resilience is moving from “better prediction” to “faster reaction.”
From insight to execution—where the gap appears
Manufacturers already capture terabytes of data through sales orders, machine telemetry, shipping schedules, and weather feeds. Problems arise when those feeds live in separate systems.
A purchasing team may spot an incoming spike in consumer demand, yet the information reaches the factory planner days later—after raw-material buffers have run dry and overtime rosters are locked. The execution lag converts a small forecasting error into a production stoppage.
Think about the sudden 40% jump in export orders when a competitor’s plant went offline. Its legacy planning tool may flag the uptick, but the message never reached the trucking partner responsible for hauling finished goods to port. Container slots may be missed, air-freight costs through the roof and overtime erases the profit margin of the surprise orders.
The lesson is blunt: a forecast is only as valuable as the supply-chain nerve system that acts on it in real time. Indeed, building a “decision loop” instead of a crystal ball and a resilient Asian supply chain needs three continuous loops rather than one periodic forecast.
First, real-time visibility. Factory, warehouse and transport data must feed into a single monitoring layer that updates as conditions change. That layer should track not only inventory levels but also capacity constraints—dock doors, trailer availability, skilled labour shifts and even local customs-clearing speed.
The second is scenario simulation. The monitoring layer must trigger automated “what-if” models the moment it detects a deviation. If a typhoon delays feeder vessels in the South China Sea, for example, the system should immediately test alternative routings through to alternative ports such as Port Klang or Batam. This presents a cost-to-serve comparison to the planner, not just an alarm bell.
Thirdly, once the planner confirms the best option, purchase orders, transport bookings and labour allocations flow directly to downstream partners’ systems. No PDF attachments, no manual re-keying, no chain of missed phone calls at 2 am.
A control-tower case in action
For large Asian industrial conglomerates, spanning raw-material procurement to finished-goods exports can mean an uncomfortable reality when decision-makers are unable to obtain a single view of what was happening in their own network. Data fragmentation can force managers to spend days reconciling spreadsheets before any action is taken.
Using integrated logistics control towers that ingest transaction data from suppliers, inland depots, port terminals and over-the-road fleets are essential in such situations. Routine data-processing tasks that once required a week can be completed in hours, and more importantly, the control tower enables proactive risk flags.
This leads to shortage risks, capacity gaps, and congestion alerts appeared before service levels deteriorated. Inventory carrying costs fell and order-to-cash cycles shortened.
From seasonal planning to perpetual alignment
Traditional planning treats the supply chain like plumbing, setting the valves in advance and watching the flow. That metaphor breaks when consumer tastes evolve faster than tooling can be re-set.
A shoe manufacturer serving Southeast Asian e-commerce platforms, for example, now sees micro-influencer posts shift demand patterns within a single weekend. A digital-first supply chain picks up sales signals directly from online marketplaces and triggers factory changeovers or postponement strategies automatically.
Where forecasting still matters
None of this dismisses forward-looking models. Long-range forecasts remain vital for capital-equipment sizing, contract negotiations and workforce development.
The difference is that short-term operations cannot depend solely on a twelve-month S&OP (Sales & Operations Planning) file. Instead, execution systems must respond continuously, whilst planners treat forecasts as just one input in an always-on optimisation engine.
Technology without silos
Much of the technology needed already exists such as cloud data lakes, advanced optimisation algorithms and artificial intelligence-powered demand sensing. Yet adoption often stalls when IT projects replicate the very silos they aimed to break.
Successful manufacturers start small using the highest-impact data sources (often order feeds and transport events) to a unified visibility layer, prove value in one product line, then scale.
Cost is no longer the dominant barrier. What matters more is change management where aligning key performance indicators across procurement, production and logistics, so that a decision benefiting one node, does not harm the wider network. When everyone measures on-time-in-full at total landed cost, collaboration beats functional optimisation.
The evolving role of factories in Asia
As reshoring and “China + 1” strategies redraw the production map, factories in Thailand, India, and Indonesia are handling product mixes that change quarter by quarter.
Real-time intelligence lets these plants pivot from one stock keeping unit cluster to another without bloating safety stock. A digital control tower that links offshore suppliers with near-port assembly hubs can orchestrate this pivot at lower carbon and cash cost than a spreadsheet ever could.
Looking forward—resilience as competitive advantage
Manufacturing leaders in Asia increasingly rate supply-chain resilience on par with cost per unit.
Corporate boards may ask, how quickly can we swap a supplier, reroute a shipment or change a bill of materials without missing orders? The companies that answer “hours, not weeks” will capture market share whenever the next shock hits.
Those still polishing their forecast accuracy to the second decimal place may discover that yesterday’s perfectly predicted demand is today’s unshipped backlog.
Resilience is not a premium feature reserved for crises; it is a day-to-day operating model. When supply chains become digital nervous systems—sensing, deciding and acting in near real time—forecasting finds its rightful place: a helpful guide, not the single point of failure.