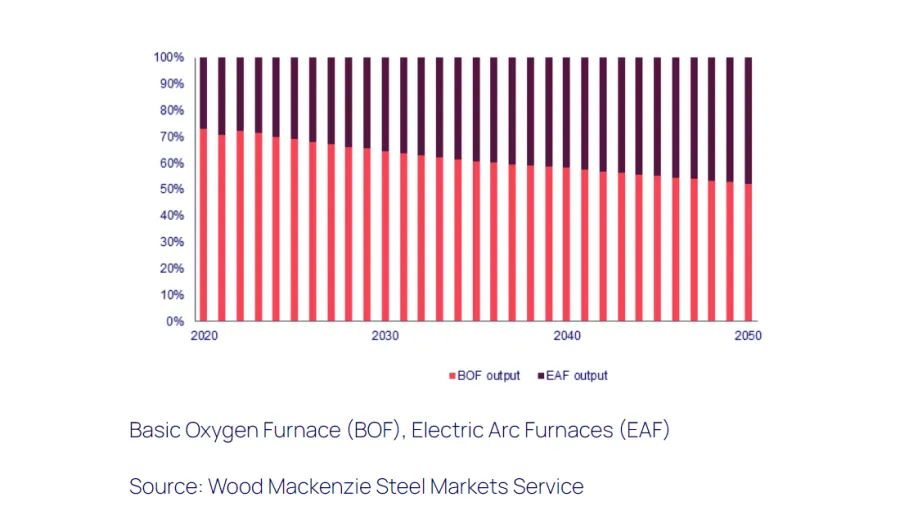
Steel sector decarbonisation put zinc circularity at risk: expert
Steel dust from traditional electric arc furnaces contains 17% of zinc.
Green hydrogen-based direct reduced iron (DRI) is key to significantly reducing the carbon emissions of steelmaking globally, but the process poses a challenge for the zinc market, according to Wood Mackenzie.
In a recent report, the data analytics firm warned that a widespread shift to using more DRI in electric arc furnaces (EAF) versus scrap steel could result in lower zinc content in EAF dust, increasing the cost and carbon intensity of zinc recovery.
Its estimates showed the existing EAF process yields 535 million tonnes of steel each year with the steel dust created during the process containing from 200,000 to 3.4 million tonnes of zinc. EAF dust contains 17% of zinc on average, and steel dust and other residues from the process alone already supply 1.6 million tonnes of zinc globally.
Wood Mackenzie’s head of zinc markets, Andrew Thomas, projected that nearly half of the world’s steel supply will be processed in EAF and a broader shift to hydrogen-based DRI EAF steelmaking could raise concerns to the zinc market.
The report noted that the latest technology available for zinc recovery and recycling has already been proven as highly carbon-intensive, a major barrier for the industry’s own decarbonisation goals.
“Alternative methods of recovering zinc from steel dusts have proven unsuccessful, posing a risk that the steel industry’s decarbonisation efforts and rising carbon costs could inadvertently hinder the circularity of zinc,” said Thomas.